電漿蝕刻技術自1970年代應用於半導體製造以來,已成為產業中相當關鍵的一核心技術,相較於濕式蝕刻製程可能產生的水汙染問題,乾式的電漿蝕刻技術更符合現今的綠色製造要求,其應用範疇也逐步擴及到先進封裝、PCB產業、光電產業、Micro LED、MEMS(Micro Electro Mechanical Systems;微機電系統)等領域。為進一步符合現代的微小細線路及高度的電性要求,其對於電漿源的控制、電場的設計與模擬、包含製程氣體比例在內的製程配方等要求也日益複雜化,形成一需要厚積知識及實驗數據的產業,並高度仰賴量產前的打樣測試與樣品分析。以下針對凌嘉科技所掌握之電漿製程設備能力進行簡述:
- Surface Cleaning/Metal Oxide Reduction(表面清潔/去除氧化層)
- 將材料置於真空腔體內,再以電漿解離產生的帶電離子(如Ar+)撞擊表面上的污染物或氧化層,將其從材料表面剝離後,再透過真空泵浦抽出,達到材料表面清潔或去除氧化層的目的。
- Surface Activation/ Surface Modification(表面活化/表面改質)
- 利用電漿技術使材料表面發生化學反應,進而改善材料表面特性的一種方法。例如增加材料表面附著力時,即是以電漿解離產生的帶電離子轟擊材料表面,並使表層的分子結構發生改變,從而增加表面附著力和親和力。
- Descum/Photoresist Stripping(除膠渣/光阻去除)
- 曝光顯影製程會使用光阻剝離劑(PR Stripper)去除不必要的光阻劑,但仍可能有未完全去除的光阻劑殘留在材料表面,這些殘留物可能會干擾後續的線路圖案解析,進而影響產品性能。而電漿蝕刻就是一種有效將殘留薄膜去除的方法。其是於高真空狀態下,配合特定比例的製程氣體、特定的電漿電源控制方式與參數,及優異的電場配置等關鍵技術,藉此產生具高等向性的電漿或飽和且均勻分布的自由基,進而將材料表面的污染物物理擊碎或化學去除。這種方法具有高效、環保、再現性高等優點,能確保後續工藝的可靠進行。
- Desmear/Etch Back/Via Formation/Trench Formation(除膠渣/回蝕/孔成形/溝槽成形)
- 於PCB製程中以雷射或其他方法於材料上形成孔洞(Via)或溝槽(Trench)時,仍可能殘留膠渣或碳渣。此時藉由電漿蝕刻設備的高選擇比特性,能妥善地去除孔或溝槽底部及側邊的殘渣(Desmear),進一步還能蝕去孔壁或溝槽壁的部分介電層並使銅層(Etch Back)局部裸露,讓後製程的銅層能良好的附著於孔壁或溝槽壁上而達到優異的電性表現。
- High Aspect Ratio Application(高深寬比應用)
- 藉由凌嘉科技獨家的硬體配置搭配特殊的先進控制方式,能有效減少待蝕刻物因為自身來料狀態或因溫度變化而導致的變形,使待蝕刻物始終維持優異的平整度,進而輔以高能量的電漿源及高非等向性的電場控制達到優異的高縱深比蝕刻。
- Metal Etching(金屬層蝕刻)
- 因製程要求而需移除材料表面例如種子層等金屬層時,由於其金屬原子的晶格特性,使得單以物理性電漿蝕刻技術並無法有效的將其去除,亦有可能在去除時傷害到底層的材料,因此輔以化學性電漿蝕刻技術即為去除金屬層的關鍵技術。凌嘉科技掌握獨有的製程配方,能有效依據不同的金屬材質適配不同的處理方式,達到優異的蝕刻表現。
- Dielectric Thin Down(介電層減薄)
- 當不斷嘗試縮小封裝尺寸時,除了縮小線寬線距的同時,減薄ABF材料並使其具有較薄的厚度亦是通用的做法之一。凌嘉科技的化學性電漿蝕刻設備符合此製程的需要,能實現均勻減薄介電層之目的。
- Remove Sacrificial Layer(去除犧牲層)
- 於MEMS的製造過程中,因其結構特性需先設置犧牲層(Sacrificial Layer),再於金屬層的立體結構成型後將其移除並形成間隙。惟此時的犧牲層多被金屬層所覆蓋。選用適當的製程氣體,並以高選擇比蝕刻的方式去除犧牲層即能妥善完成此製程目的。
對此,凌嘉科技有自主的智慧財產權及豐富的製程開發經驗,熟稔電漿蝕刻技術的ICP、CCP、RIE、HDP、RPS、ESC等關鍵技術,並擁有自主的配方知識庫能適當的依材料特性選擇合適的製程配置,亦能協同客戶進行製程開發及實驗驗證,除了可以提供研發階段於不同製程配方下的打樣服務之外,亦擁有合格且高精密度的實驗室能進行樣品的測試。
產品系列 PISCES® Family
Model |
PC series |
PD series |
PE series |
PF series |
Schematic |
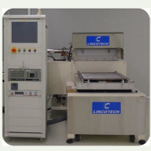 |
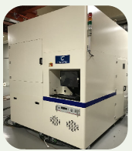 |
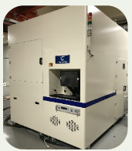 |
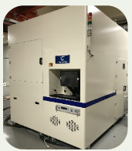 |
Application |
Surface cleaning
Surface modification
Surface activation
Metal oxide reduction |
Desmear
Descum
Metal etch
Oxide etch
Surface shape control |
Dielectric thin down
Etch back
PR stripping
Remove sacrificial layer |
Via formation
Trench formation
High AR desmear
Fine line etching |